Submerged arc welding is ideal for pipelines, pressure vessels and tanks, rail fabrication and major construction applications, with the simplest monofilament form, double wire structure, tandem double wire structure and multi-filament structure.
Submerged arc welding can benefit users in many welding applications. From increasing productivity, to improving the working environment, to ensuring consistent quality and more. Metal processing fabricators that are considering changes in the submerged arc welding process should have thought that they can get a lot of benefits from this process.
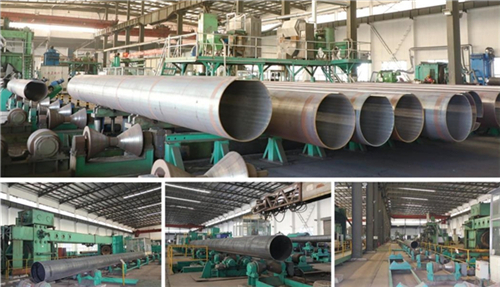
Basic knowledge of submerged arc welding
The submerged arc welding process is a requirement suitable for heavy industrial applications such as pipes, pressure vessels and tanks, locomotive construction, heavy construction/excavation. Ideal for industries that require high productivity, especially when it comes to welding very thick materials, there are many benefits to be gained from the submerged arc welding process.
Its high deposition rate and walking speed can have a significant impact on worker productivity, efficiency and production costs, which is one of the key advantages of the submerged arc welding process.
Other benefits include: excellent chemical composition and mechanical properties of the weld, minimal arc visibility and low welding fumes, improved working environment comfort, and good weld shape and toe line.
Submerged arc welding is a wire feeding mechanism that uses granular flux to separate the arc from the air, as the name suggests, the arc is buried in the flux, which means that when the parameters are set, the arc is invisible with the outflow of a layer of flux. The welding wire is fed continuously by a torch that moves along the weld.
Arc heating melts a section of the wire, part of the flux and the base metal, forming a molten pool, which condenses to form a weld covered with a layer of welding slag. The thickness range of welding material is 1/16"-3/4", can be 100% penetration welding by single welding, if the wall thickness is not limited, multi-pass welding can be performed, and the weld is appropriately pretreated and selected, and the appropriate welding wire flux combination is selected.
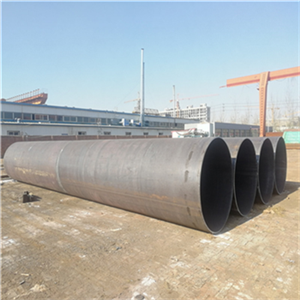
LSAW
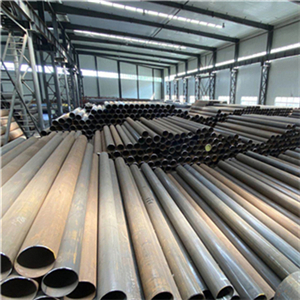
ERW

SSAW
Selection of flux and welding wire
Choosing the right flux and wire for a particular submerged arc welding process is critical to achieving the best results using the process. While submerged arc welding processes alone are efficient, productivity and efficiency can be increased even based on the welding wire and flux used.
The flux not only protects the weld pool, but also contributes to the improvement of the mechanical properties and productivity of the weld. The formulation of fluxes has a huge impact on these factors, affecting current carrying capacity and slag release.
The current carrying capacity means that the highest possible deposition efficiency and high-quality weld profile can be obtained.
Slag release from a particular flux affects flux selection because some fluxes are more suitable for certain solder designs than others.
Flux selection options for submerged arc soldering include active and neutral types of welds. A fundamental difference is that the active flux changes the chemistry of the weld, while the neutral flux does not.
Active fluxes are characterized by the inclusion of silicon and manganese. These elements help maintain the tensile strength of the weld at high heat input, help keep the weld smooth and smooth at high travel speeds and provide good slag release. Overall, active fluxes can help reduce the risk of poor solder quality, as well as expensive post-weld cleaning and rework. Keep in mind, however, that active fluxes are usually best suited for single- or double-pass soldering.
Neutral fluxes are better for large multipass solders because they help avoid the formation of brittle, crack-sensitive welds.
There are many types of welding wire choices regarding submerged arc welding, each with advantages and disadvantages. Some wires are formulated for welding at higher heat inputs, while others are specifically designed to have alloys that help the flux to perform welding cleaning.
Note that the chemical properties and heat input interaction of the welding wire affect the mechanical properties of the weld. Productivity can also be greatly increased by filler metal selection.
For example, using a metal core wire with a submerged arc welding process can increase the deposition efficiency by 15% to 30% compared to using solid wire, while also providing a wider and shallower penetration profile.
Due to its high travel speed, metal core wires also reduce heat input to minimize the risk of welding deformation and burnout.
Of all steels, austenitic stainless steels have the lowest yield point. Therefore, in terms of mechanical properties, austenitic stainless steel is not the best material for the valve stem, because to ensure a certain strength, the diameter of the valve stem will increase. The yield point cannot be increased by heat treatment, but it can be increased by cold forming.
We are stockist of carbon and stainless seamless steel pipe ,welcome any enquiries , we will offer in the first time!
Post time: Jan-30-2023